An increasingly sustainable society, with a close interdependence between man and the environment and a new approach to the future. To achieve this, we need to work to make the transition towards this type of development real and substantial. A commitment that also involves mobility, which must necessarily direct its efforts and energies in this direction.
The main purpose of LiBER PROJECT, The main purpose of co-financed under the POR – FESR 2014 – 2020 of the Emilia-Romagna Region, whose main partners are the University of Bologna, various industrial research departments and laboratories and some regional companies operating in the product/process development sector and in the use of battery packs for different applications, is the sustainable development of society.
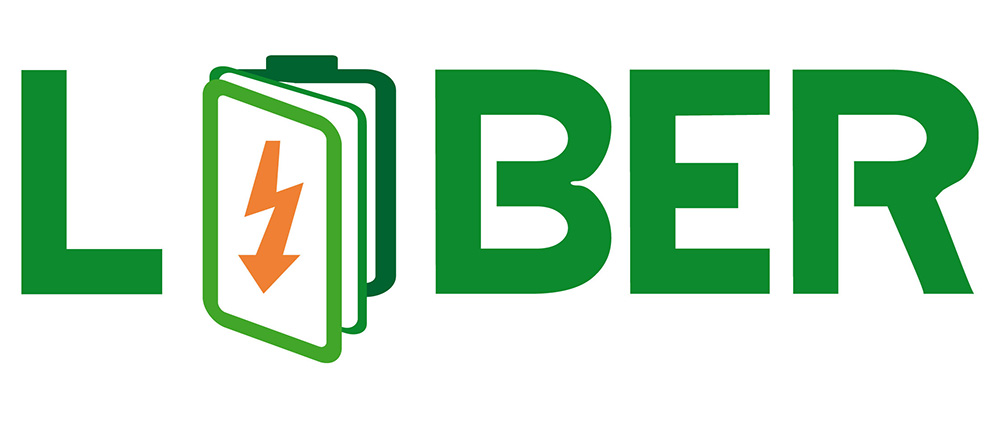
In fact, LiBER aims to create technological systems complete with battery packs (BP), consisting of a significant number of cylindrical cells (tens of thousands) starting from basic modules, produced with an automated and qualified process, for automotive and industrial handling in Emilia-Romagna, able to be used in countless application areas.
It is a robotic station (3 robots: Cartesian, delta and anthropomorphic) for the construction of battery packs, which begins with the assembly process of basic modules (bricks) produced with an automated and qualified process.
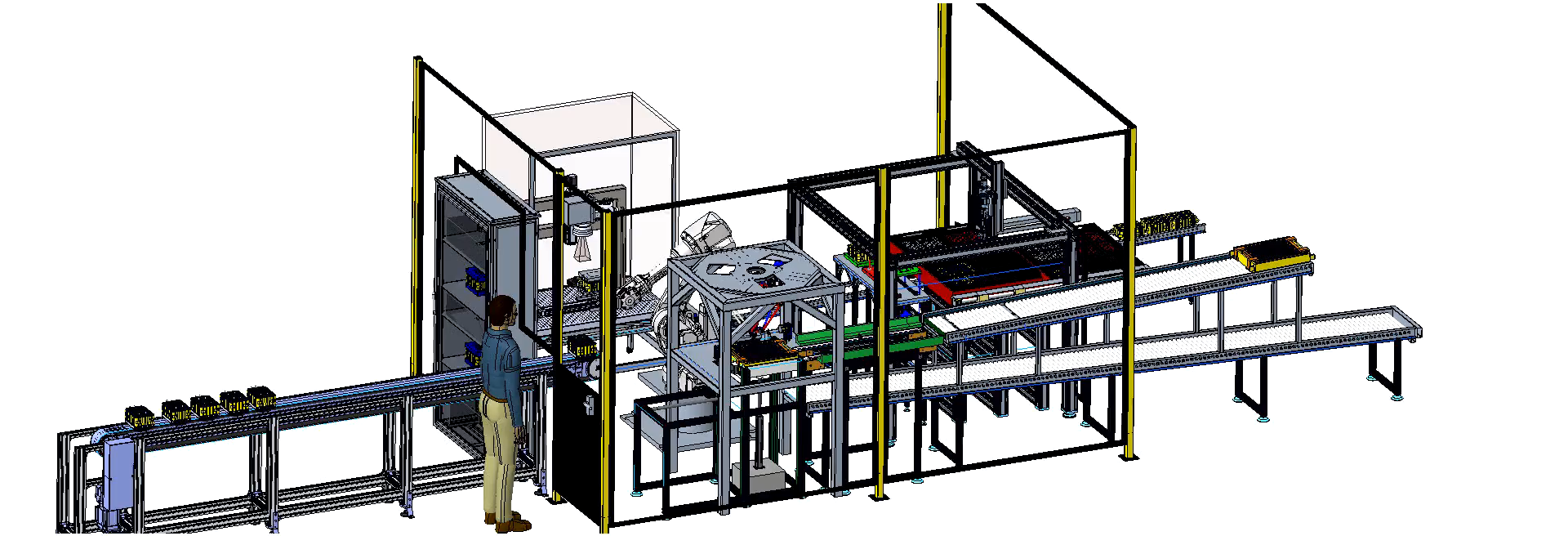
Flessibilità, approccio modulare, economicità, sicurezza, capacità diagnostica locale e remota, facilità di integrazione e di recupero e riutilizzo a fine vita sono le caratteristiche principali di questa soluzione.
Caratteristiche che, ad oggi, non si potevano ottenere con le soluzioni presenti in commercio.
L’approccio modulare, reso possibile con la linea a pallet liberi, garantisce una maggiore produttività, mentre la programmazione Isole di lavoro asservite da robot antropomorfo consentono una semplice integrazione in spazi ristretti e una manipolazione precisa e versatile.
Il brick assemblato è personalizzabile per potersi adattare a diverse geometrie di pacco e, quindi, per essere installato su diverse applicazioni mobili.
Ad esempio, veicoli commerciali, autobus, macchine agricole, mezzi da costruzione.
Il brick può essere installato anche su applicazioni stazionarie quali i sistemi di accumulo combinati a fonti rinnovabili e gli UPS.
La soluzione LiBER garantisce un monitoraggio evoluto: è infatti possibile monitorare la temperatura di ogni cella (a differenza di pacchi di batteria tradizionali dove viene presa la temperatura in zone o del liquido di raffreddamento).
Questa soluzione determina un notevole incremento del livello di sicurezza attiva del pacco rispetto alle soluzioni in commercio.
Flexibility, modular approach, cost-effectiveness, safety, local and remote diagnostic capability, ease of integration and recovery and reuse at the end of life are the main features of this solution. Features that, to date, could not be obtained with the solutions available on the market.
The modular approach, made possible with the free pallet line, guarantees greater productivity, while the programming of work islands serviced by anthropomorphic robots allow for simple integration in confined spaces and precise and versatile handling.
The assembled brick is customisable to be able to adapt to different pack geometries and, therefore, to be installed on different mobile applications. For example, commercial vehicles, buses, agricultural machinery, construction vehicles. The brick can also be installed on stationary applications such as storage systems combined with renewable sources and UPS.
The LiBER solution guarantees advanced monitoring: it is in fact possible to monitor the temperature of each cell (unlike traditional battery packs where the temperature in zones or the coolant is measured).
This solution determines a considerable increase in the level of active safety of the pack compared to the solutions on the market. Furthermore, the data collected, crossed with the depletion time and combined with the driving style, will allow for considerable information, in order to optimise the management of the battery itself during its entire life.
Advanced monitoring and design planned to facilitate disassembly will allow the battery to be exploited in ‘second-life’ applications once the battery has been used on the native application.
LiBER will develop the whole process, in order to provide validated solutions with a high level of development and qualification and speed up the industrialisation phase and safe introduction on the market.
This will supply the regional automotive sector with innovative complete battery pack product solutions currently not found in the regional production sector, but will also offer new industrial sectors (hybrid and electric cars/motorcycles and electric work vehicles), product and process solutions for advanced BPs.
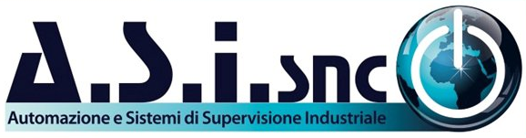
Furthermore, ASI S.N.C., System Integrator and Te.Co. customer which studies custom solutions by choosing the most suitable components for the required needs, has carried out the study and will design the construction of the robotic island. The machine will be part of a much more complex project, in which a new university spin-off will play an active part, relating to green public transport and will be exhibited at the university itself.
Two very important Te.Co. partners are collaborating on the LiBER Project by providing the necessary components for the development: Datalogic and Rockwell Automation.
Datalogic system components:
- MATRIX220 7mm reader the robot takes the battery from the box and presents it to the reader and starts rotating it until the code is read
- 10 ” taskbook, machine HMI, operator panel, also useful for remote tasks thanks to the versatility of use as a tablet
Rockwell Automation components
- PLC and drives
This project started in 2017 in the University of Bologna laboratories and was patented the following year. In 2020, despite the pandemic and related difficulties, LiBER made the first prototypes to be tested.
In this 2021 that has just begun, the focus is instead on the industrial phase and the creation of a Start Up to create localised battery production lines, i.e. installed directly within the companies that will use them, but which will all be part of the pilot line, managed and controlled by UNIBO.